I don't even text or have a cell phone to text with but I do know what OMG stands for. On one hand I think we should congratulate Lupe on the wonderful pictures she supplies for the blog but on the other hand (mine) it takes a lot of time to download them, put them into iPhoto, edit, crop, and then select which of them to put into the blog. Beautiful photographs Lupe, is that a new camera?
We had another fantastic turn out this month, you can see we're all enjoying each others company as we wait for the start of the meeting. I counted about 28 of you there but may have missed one or two that snuck in!
![]() |
Let's Get Started |
Several business items were brought up. One of those had to do with the MeetUp website that is paid for with our dues. Since a number of you hadn't heard of it here's a LINK to the MeetUp page for our group. You should be able to sign up by using the box on the upper, right hand corner. Once you've done that you'll get the MeetUp announcement that Jamie sends out, usually the weekend before the meeting. Then, if you're in my address book for the Sin City Woodworkers you'll get the reminder that I generally send out the Tuesday before the scheduled meeting. Jamie mentioned that she wanted 100 members on the MeetUp listing so get in there and sign up!
Another thing to keep in mind is signing up for the AWFS fair that is scheduled to be in town July 24-27. I know there's a price break if you register before the end of the month (I think) but it would be to your advantage to check their site to get the correct dates. Here's a LINK to the 2013 show information. It's definitely something to see and the educational classes have been good in the past.
One more thing to keep in mind is The Jamie 2" x 4" x 8' Challenge:
That will culminate at our Christmas meeting and can be anything you can create using just one construction grade piece of wood. You're allowed to add hardware and finish but no other materials are allowed.
![]() |
This is Crown Molding |
For the demonstration he had a Bosch, 12" compound miter saw that really made the work easier. A saw that size can easily handle the crown he was using. The first step when installing the molding on the ceiling is to figure out the distance it'll come down and mark that on the fence of the saw. Crown molding has two flat spots that you hold against the saw table and fence while cutting. He mentioned how the profile on a piece of crown can vary by 1/8"+ from one end to the other so a valuable tip was to locate the center of the piece first and measure out from there in both directions to get your length. That insures your returns will have the same profile.
![]() |
Return Matches When Measuring from Center |
Since you're measuring from an angled piece it's difficult to hook the tape measure over the end. A smart thing to do anytime is to "burn an inch, just don't forget to add it back to your measurement. I was sitting by Jamie and both of us mentioned that we burn 10", the math is easier!
![]() |
Burning an Inch |
![]() |
Mind Your Fingers! |
![]() |
Large Size |
![]() |
Hand Applied Style |
I did a quick Amazon search and they range in price from around $30.00 to well over $200.00. Here's a LINK to that search page but keep in mind that you get what you pay for. I've used a system similar to the Ulima set which is currently unavailable. They will leave a small indentation which can be taken care of with putty followed by paint or stain. A hint to make assembly more accurate is to either block plane or sand the inner edge of the miter, this is a quickie method of coping the joint but will make the final results better.
After the molding was glued and joined it was time to cut the pieces for the top, bottom, and a cleat. The first step was to glue and pin the it to the shelf. This was done upside down:
![]() |
Molding to Shelf |
![]() |
Bottom Held Proud |
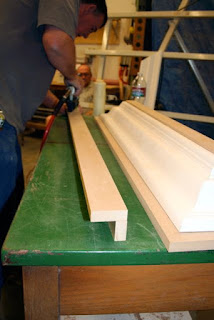
The cleat is a simple L-shaped affair that you would screw to the wall studs, the shelf will then be placed on top and either nailed or screwed to it. Besides the strength it'll give you, it's much easier to level and position the cleat to the wall than it is to fool around with the shelf while you're balanced on top of a ladder!
Lots of suggestions and information was given during this outstanding demo by Dennis. Formulas are out there for how you'd calculate the width of the molding. The one I wrote down was that the molding width should equal 3/8" for every foot of wall height. This seemed small to many but keep in mind that traditionally, crown would have another molding applied below it. What you don't want to have is an 8' ceiling height with a 12" wide crown!
![]() |
Ta-Da --- I Give You A Crown Molded Shelf! |
The remainder of our meeting was the Show & Tell portion. Several members brought in their latest work and interesting items.
![]() |
Bird House -- Where's the Hole? |
Here's what they turn these into:
![]() |
After the Art Work |
They are done in a collage style and use playing cards! If you'd like more information about these and other work that MaryJane has done here's a LINK to her blog.
A new member of the group was invited and he shared some pretty amazing carvings that he's done and also a sampling of work from Ecuador. The name of the town was brought up but I'm afraid I missed it. Apparently this town is well known for it's carvers, here are some of the items he brought in to show:
![]() |
Spoons are his work, Figurines from Ecuador |
![]() |
Close Up of Owl on Books |
![]() |
Mike's Spoons, some done, some in progress |
![]() |
Ned's Tool Tote |
We can count on Ed to bring something unusual to the meetings and he didn't disappoint us this month. There were a couple of correct guesses on this one -- it's a bunghole auger. This is used for making the hole in a beer barrel which is initially sealed tight. In case you think we're making this up, check this Wikipedia LINK.
![]() |
Bunghole Auger |
In the background are a couple of pepper grinders Ed's been making on his lathe. You can see he's really getting into laminations and he uses a ceramic grinder that's supposed to be bullet proof! It's the small, white object on the left side of the auger.
Good to see such a great turn out at the meeting and hope you enjoy this blog --- John