![]() |
Nice, panoramic shot! |
We began with a show and tell session which was pretty light this time. Let me encourage you all to bring your latest work or discovery to the meetings. Just a short (5 minutes or less) presentation to share with the others is great.
For example, Beth brought in this really nice task light she found. It was super bright and the base is magnetic which allows you to place it securely on any metal surface. It also pivots so you can direct it where needed. She purchased it at Medical and Mobility which is a medical supply store located at Teneya & Lake Mead. It was mentioned that McFadden Dale on Decatur may have it as well but a quick search didn't show the exact same model. If I recall, it's powered by 4 AAA batteries.
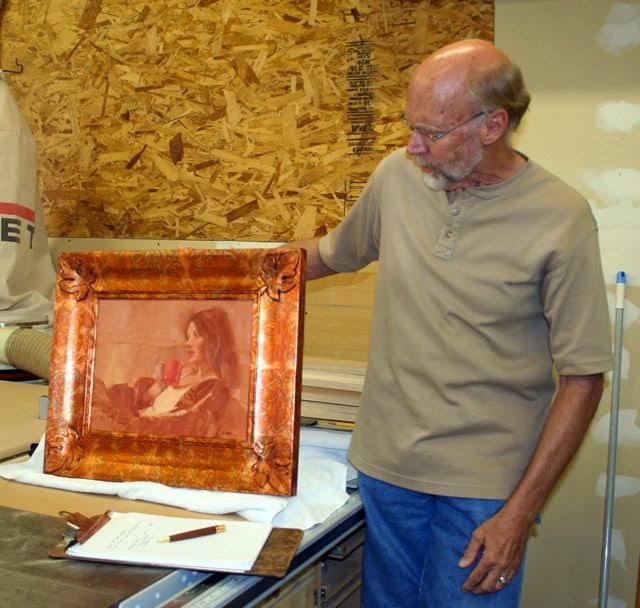
Bringing in this frame for a show and tell in Dennis's shop was a risk seeing how he holds the position of "esteemed woodcarver" in our group but I thought I'd take a chance anyway! This is a frame I carved for one of Diane's latest paintings. The corners feature carved fig leaves which were inspired by a fig tree we walk by on our doggie walks. I used an actual leaf as a pattern. The frame molding is about 4" wide and made of Basswood. This was my first frame where I used a variegated gold leaf for the finish and we thought it complements the painting nicely.
Our main presentation was next and Dennis was ready to show us his techniques for sharpening carving chisels and gouges. Here is his collection of oil stones and slip stones that he uses to get his tools razor sharp. If you've even taken a class from or seen any of his demonstrations you know the edge on his tools is a sharp as it's going to get! There just isn't any substitute for a sharp tool no matter what phase of woodworking you're doing --- period.
![]() |
Slip Stones and Oil Stones |
For Dennis, this process would take about 30 minutes. A point he made is that when he sharpens, he holds the tool stationary in one hand and moves the stone up and down on the cutting edge with the other. He explained that with the curved blades found on carving tools it's easier to hold the tool stationary and then move the stone around it. That's the best way to maintain the required bevel of the cutting edge. As you hone the bevel you're creating a burr on the inner side which needs to be removed. This is done with the appropriate sized slip stone and will create a very slight back bevel which is desirable anyway. Stones are only needed when first preparing a new tool or after many honings or an accidental drop on the floor! By the way, he mentioned that improper use of the tool by attempting to cut too deep or pry wood out of the cut will result in you spending more time sharpening than actually carving.
Once his tools are sharpened with the stones, he uses this set-up as he's carving. As you can see, it is a standard bench grinder with a stone on the left side. On the right side is his secret to super sharp tools --- a slotted, cardboard wheel that is charged with rouge. Woodcraft sells this sharpening system. Here's a LINK to their online listing of it. You'll notice there are a couple of different ways to buy it from them. I'm among many of his students that purchased this system after taking a class from him. It did cause an interesting discussion on grinder use. The normal rotation of a grinder has the top of the wheel coming down towards you. Whatever you're grinding is put towards the top of the wheel and the tool rest supports it to prevent it from kicking back at you. That's how the wheel at the left of this picture works. However; if you use the cardboard wheel on the right that way, the edge of your tool will catch and definitely come flying back at you much faster than you'd ever hope to get out of the way!
Here's a picture of my grinder, notice it's reversed. For safety I built an enclosure around the wheel and also marked the direction on some tape to remind myself. The only awkward thing about this set up is having to reach over the top of the machine to reach the on/off switch.
![]() |
V-Chisel or Parting Tool |
Lupe uploaded a short video on YouTube so you can see some of his techniques in action! If you've never checked these out, she has uploaded a series of video and you can subscribe to that particular channel to see all of them if you'd like. Here is the LINK to that channel and the video.
As the meeting was winding up Lupe mentioned that she wanted a tour of the house. Dennis has always been extremely interested in Victorian architecture and the inside of his home shows that. Here's a teaser, this is one of the columns supporting his patio cover. If I remember correctly, each one is made of 147 individually cut and fitted pieces! These are located outside, probably half a dozen of them.
Lupe took a whole lot of pictures which I'll put here at the bottom of this blog. They show the floors and ceilings whose patterns, incidentally match one and other. Also various pictures of the mill work, doors, and furniture that he has built over the years.
Enjoy and see you next month -- John